
接触网受电弓系统的一个新的非接触式故障诊断方法外文翻译、中英对照、英汉互译
9页1、A New Contact less Fault Diagnosis Approach for Pantograph-Catenary SystemRailway transport is one of the most important mass transportation media in the worldwide.With the development of trains speed, safety and comfort levels of railways is getting more importance day by day. Besides high level of security requirement, detection of anomaly for rail and road shall be early identified for decreasing operation and maintenance expenditures. The pantograph-catenary system has an important role for
2、collecting the current in electrical railways. The problem occurred in this system will affect the current collection performance of electrified trains. In this paper, a new image processing based technique is proposed to detect the arcing faults occurred between catenary and pantograph contact. The proposed method takes one frame from the digital camera and then the edge detection algorithm extracts the edges of pantograph. The arcing between contact wire and pantograph is detected by examining
3、 the position of contact wire of pantographs edge. INTRODUCTIONWith the development of the high-speed electrified trains, the demands for safety of railway transport come into more important. A pantograph is the most utilized component for transmission electric power from overhead wire to locomotive. To ensure the power without any problem, pantographs should maintain good contact under different train speeds. In recent times, the speeds of electrified trains have reached rather high levels. Und
4、er these speeds, maintain good contact is challenging problem. Via railroad maintenance planning based on early rail and road anomaly detection technologies, derailment accidents are prevented. Pantograph and overhead line are two fundamental components for the collection of current signals in electrified trains. The wear between pantograph and overhead wire will result with catastrophic faults. The pantograph arcing faults occurs because of below reasons.In railway systems, the pantograph is ma
《接触网受电弓系统的一个新的非接触式故障诊断方法外文翻译、中英对照、英汉互译》由会员公****分享,可在线阅读,更多相关《接触网受电弓系统的一个新的非接触式故障诊断方法外文翻译、中英对照、英汉互译》请在金锄头文库上搜索。
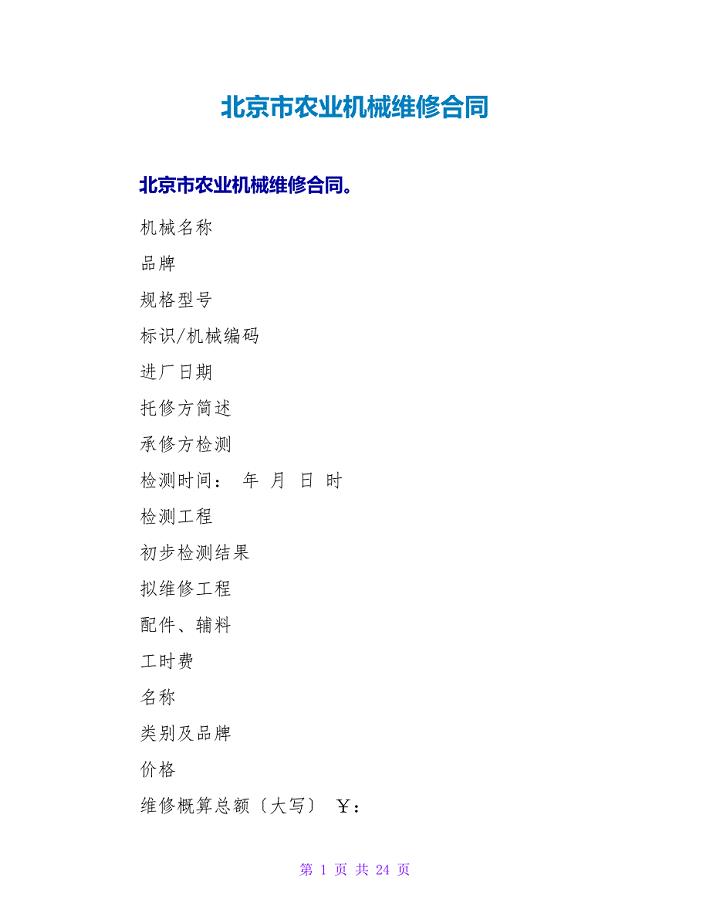
北京市农业机械维修合同.doc
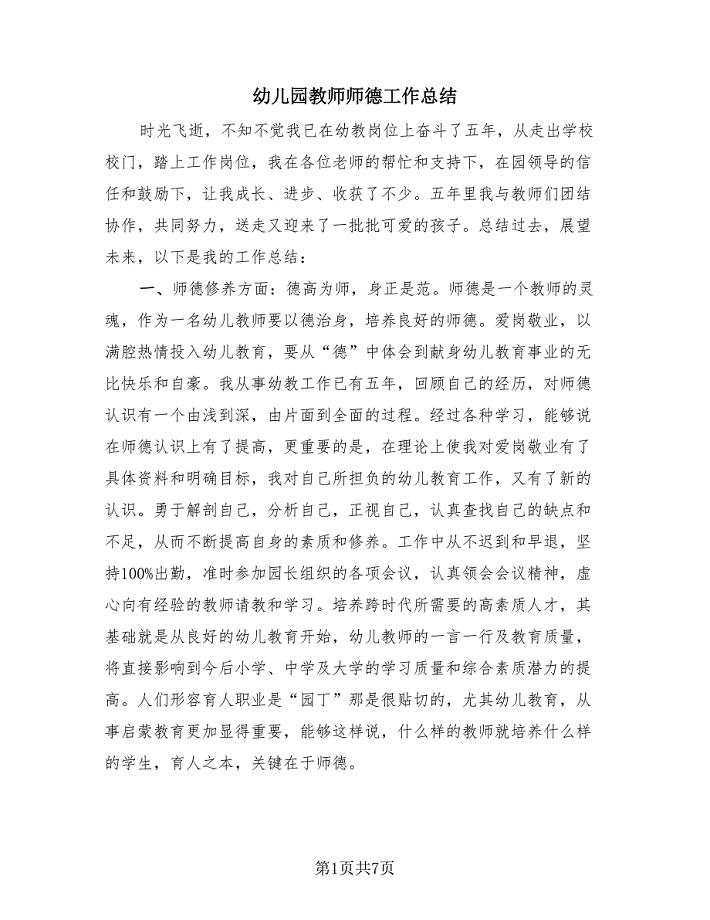
幼儿园教师师德工作总结(3篇).doc
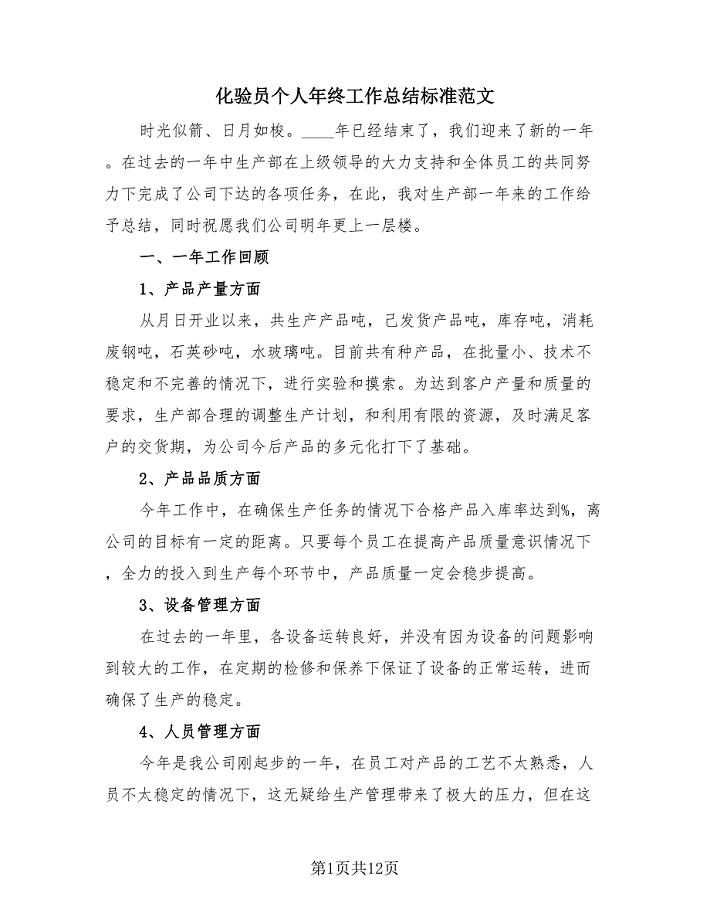
化验员个人年终工作总结标准范文(4篇).doc
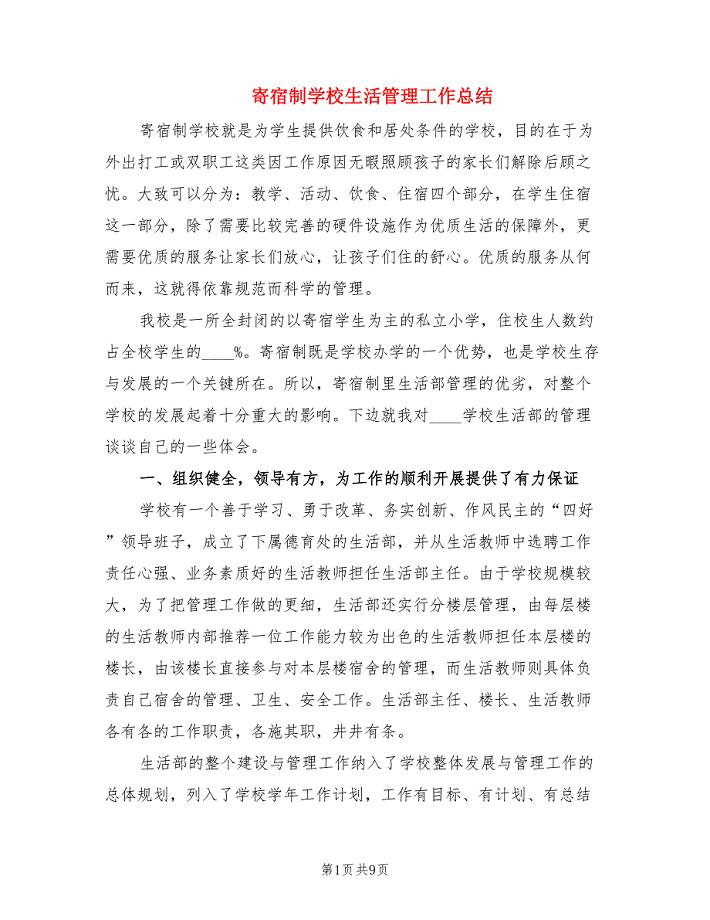
寄宿制学校生活管理工作总结(2篇).doc
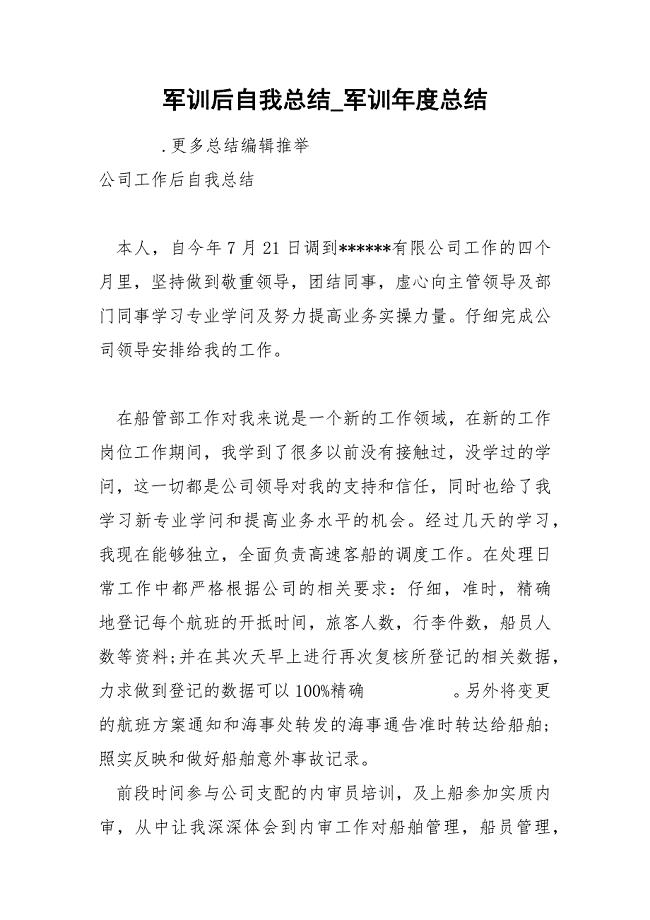
军训后自我总结
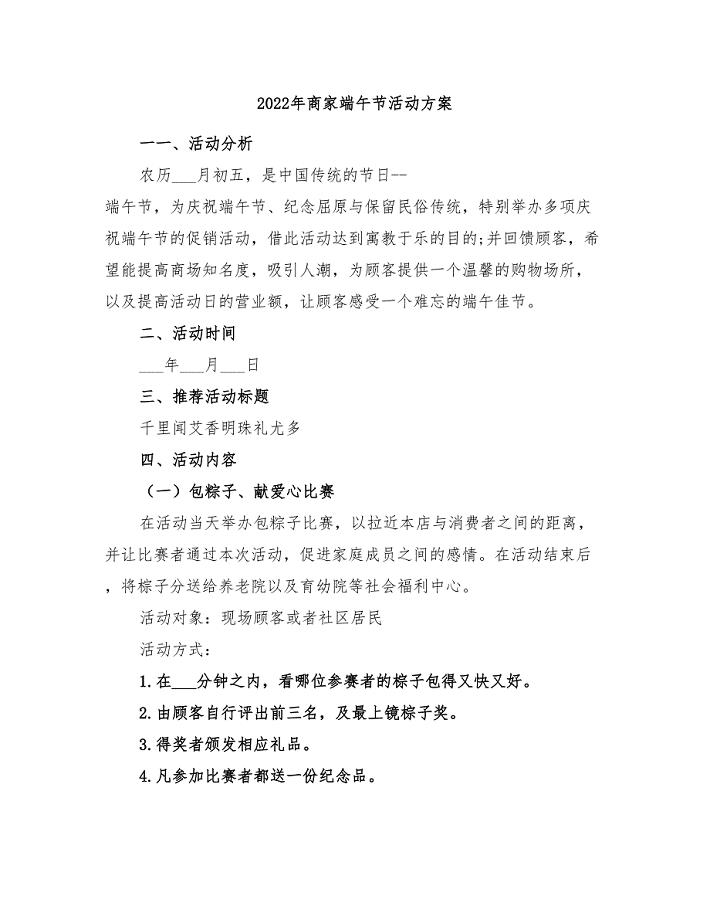
2022年商家端午节活动方案
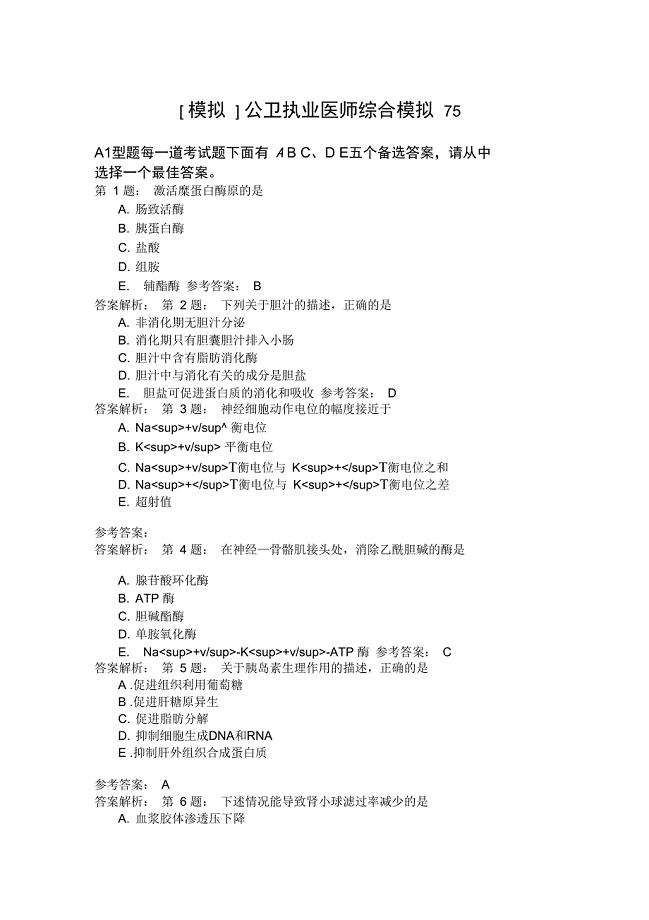
公卫执业医师综合模拟75
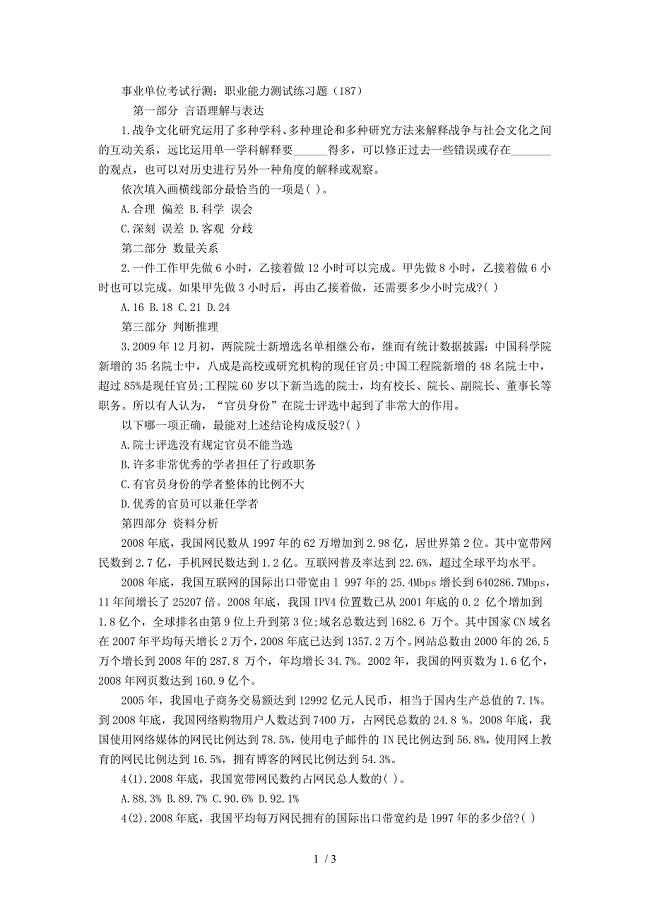
事业单位考试行测职业能力测试练习题(187)
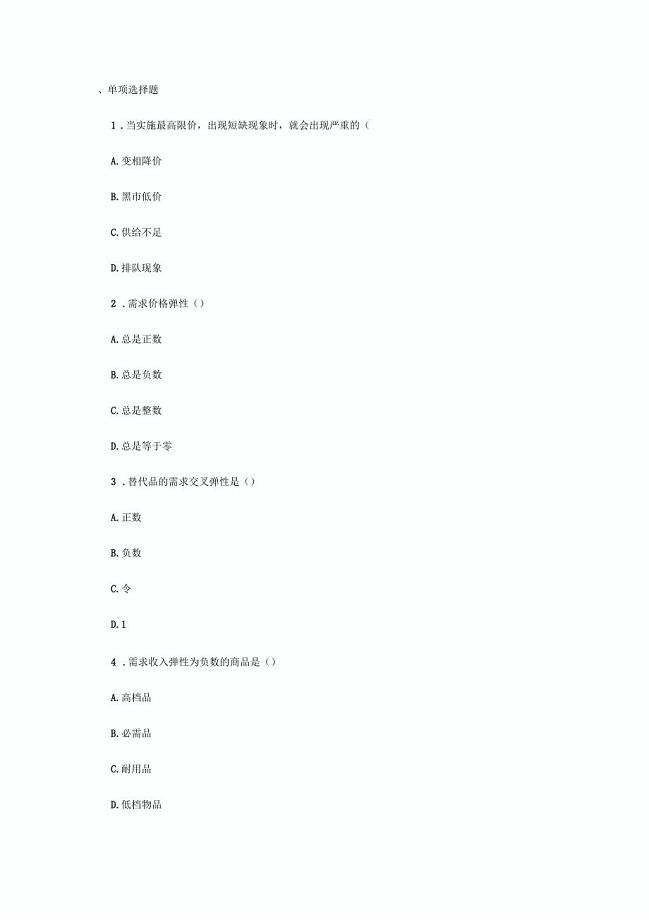
2021年经济师考试经济基础模拟试题(四)

2023年大学团支书工作总结.doc
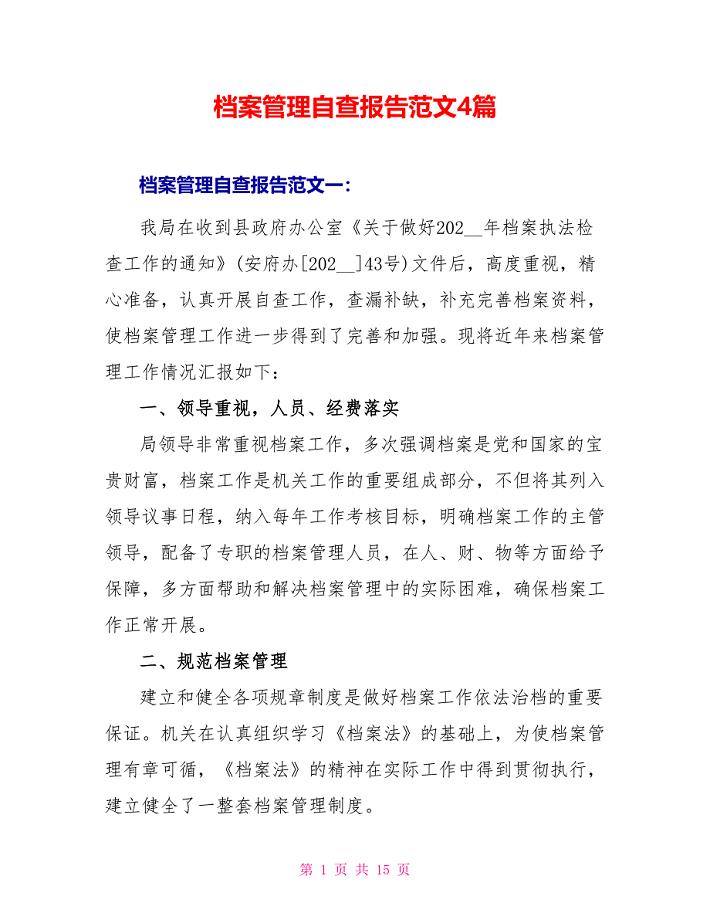
档案管理自查报告范文4篇
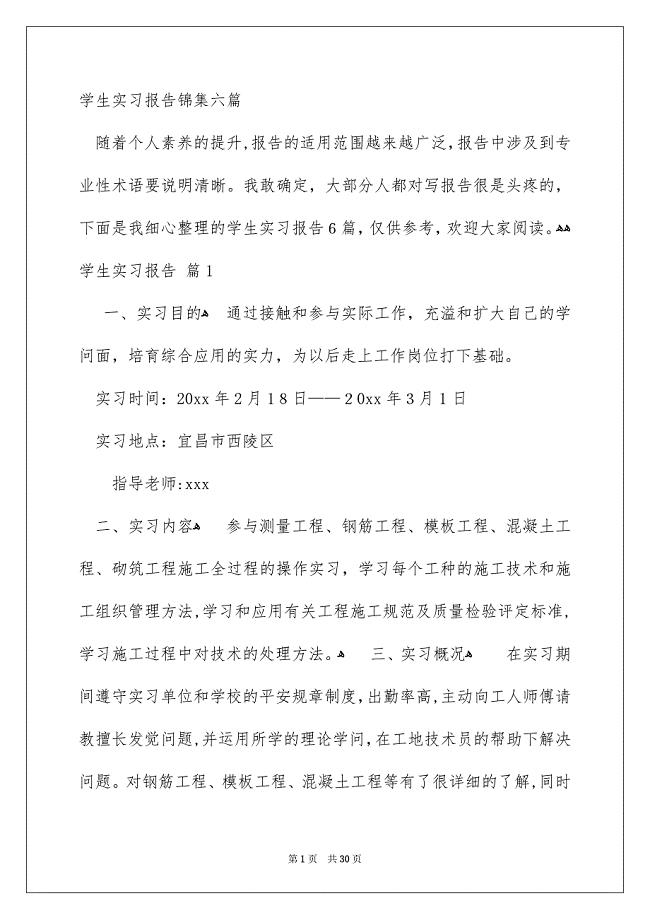
学生实习报告锦集六篇
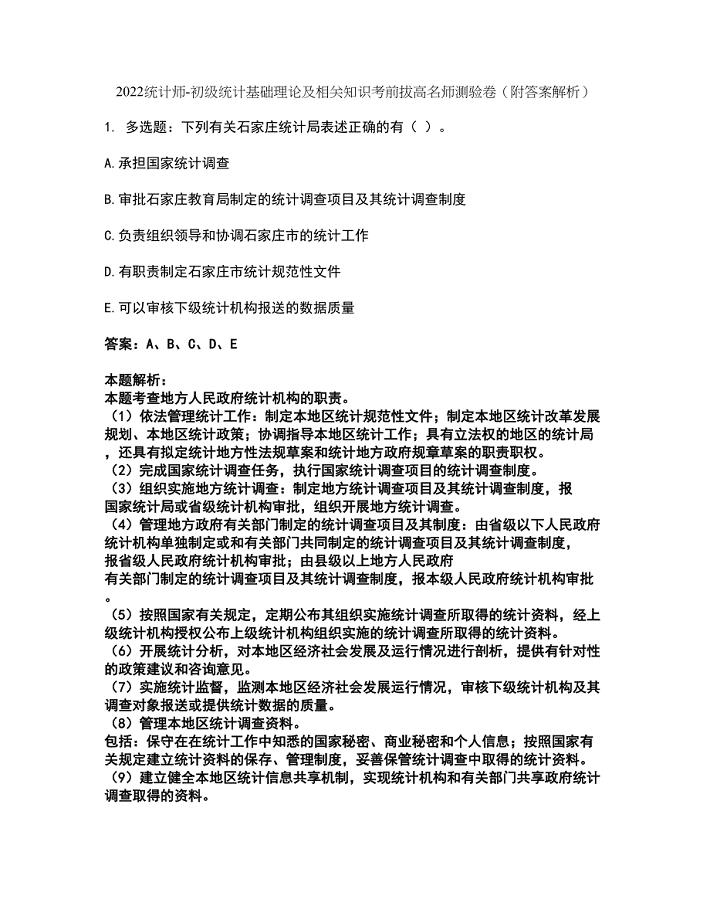
2022统计师-初级统计基础理论及相关知识考前拔高名师测验卷39(附答案解析)
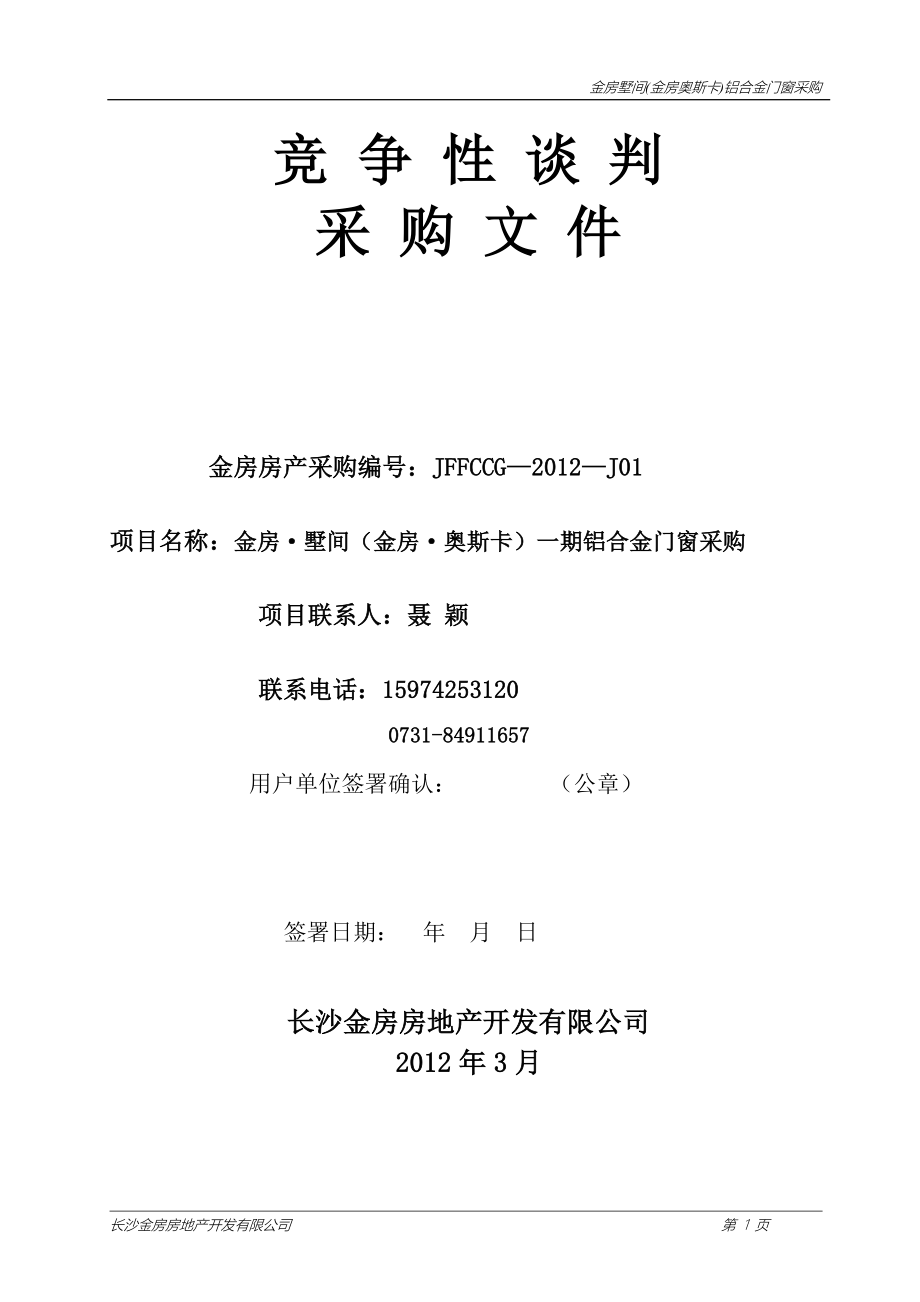
金房墅间(金房奥斯卡)铝合金门窗采购竞争性谈判采购文件
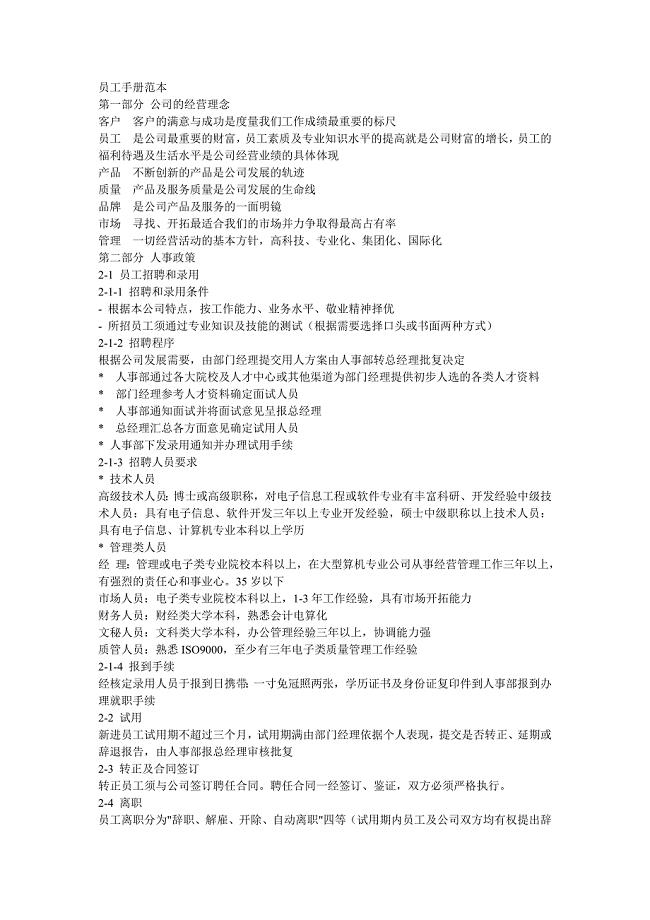
2-1员工手册范本
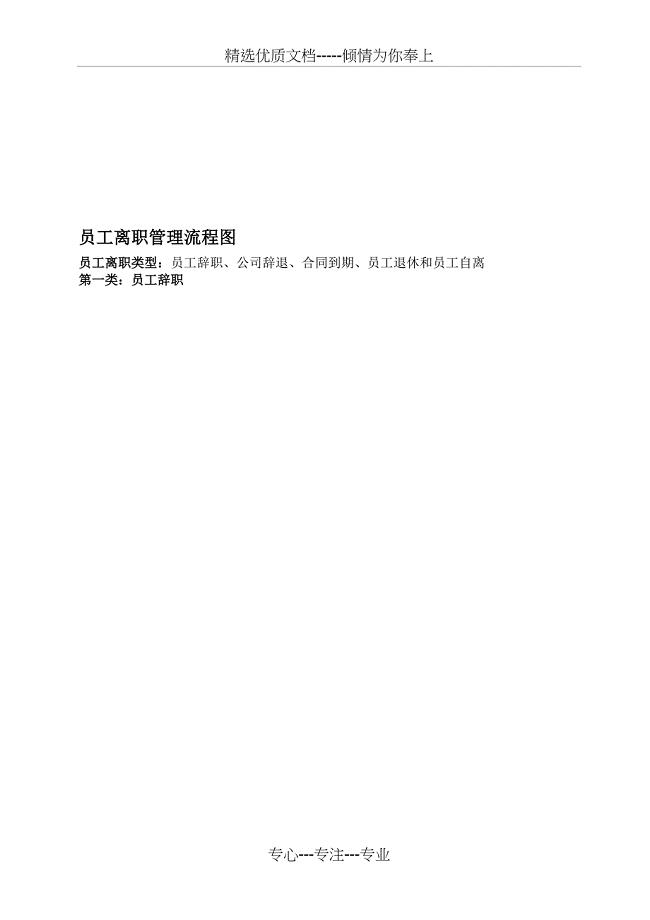
员工离职管理流程图(共6页)
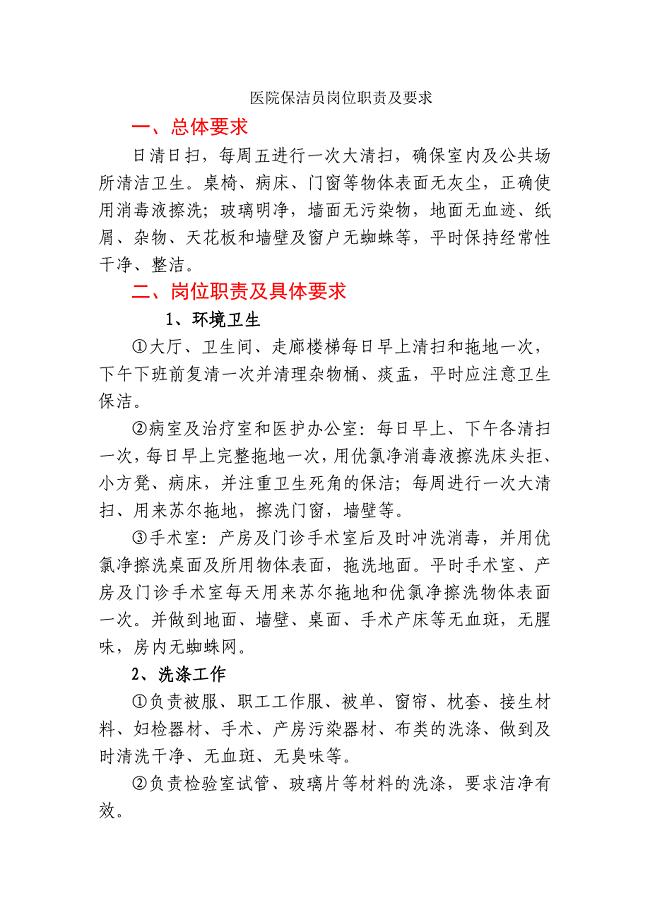
医院保洁员岗位职责及要求
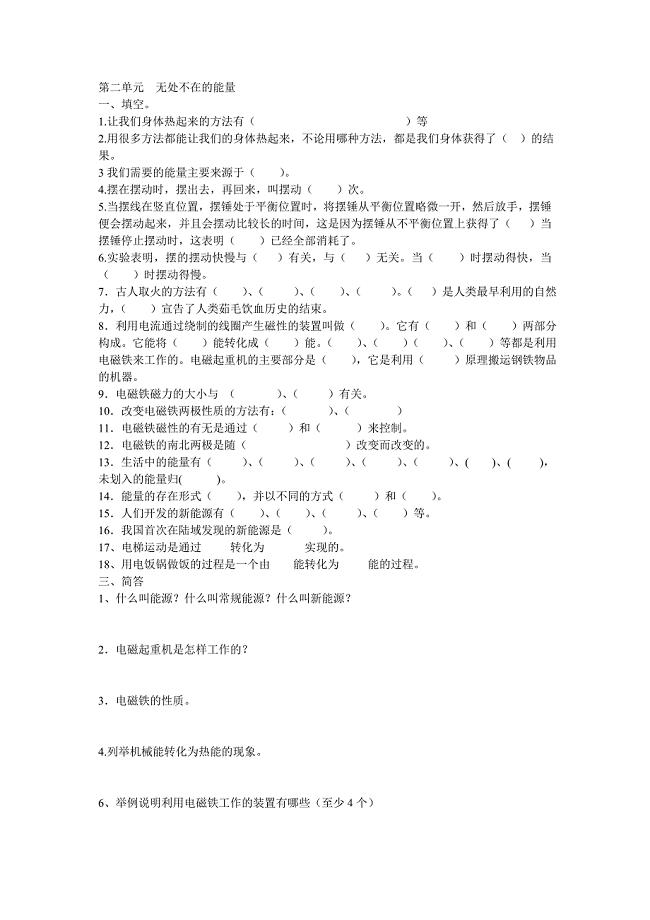
青岛版六年级下科学第二单元测试题
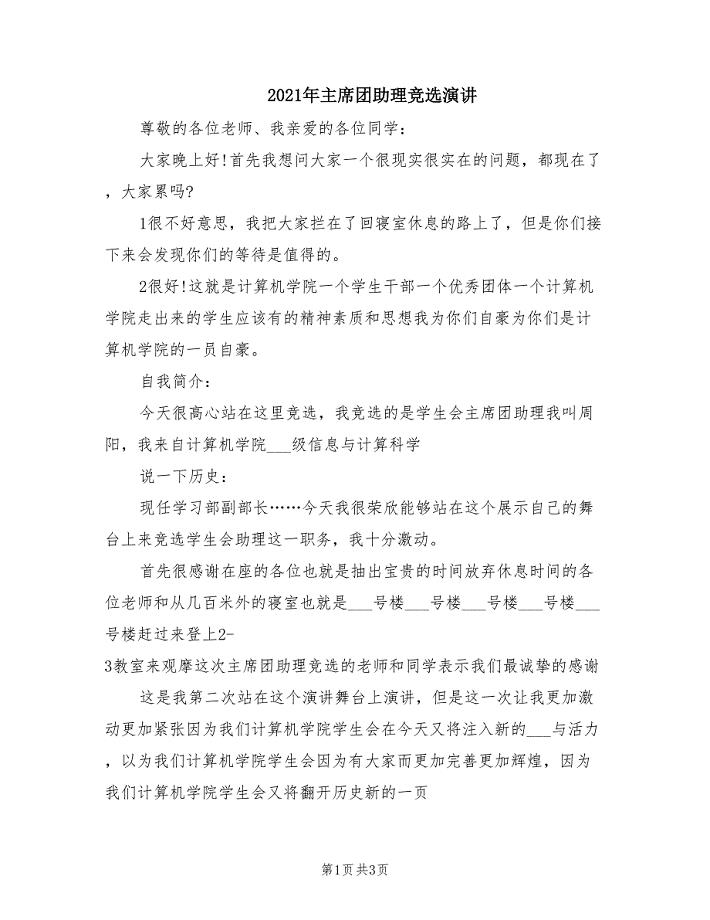
2021年主席团助理竞选演讲.doc
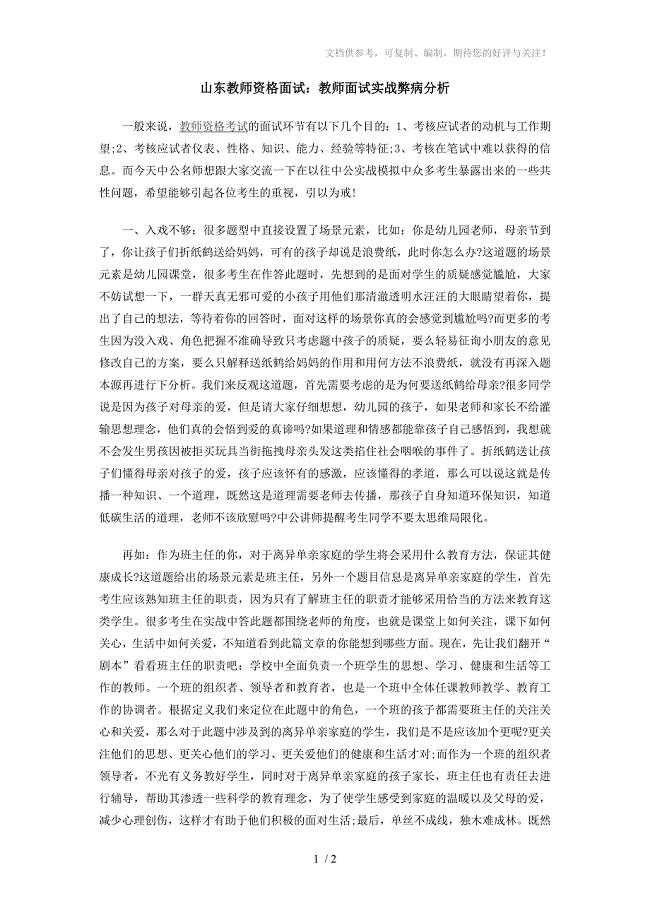
山东教师资格面试教师面试实战弊病分析

2023-03-26 14页

2023-02-07 53页

2023-01-30 24页

2023-02-16 4页

2022-12-14 12页

2023-10-08 28页

2024-01-20 11页

2023-11-13 20页

2023-10-04 5页

2022-10-11 74页